First, the principle of ultrasonic welding
Ultrasonic welding is the use of high frequency vibration wave transfer to the surface of two objects to be welded, in the case of pressure, so that the two surface friction and the formation of molecular layer between the fusion.
The main components of an ultrasonic welding system include:
Ultrasonic Generator/Transducer/Lock/Welding Triple/Mold and Rack. Ultrasonic welding uses an ultrasonic generator to convert a 50/60Hz current into 15, 20, 30 or 40 kHz energy.
The converted high-frequency electrical energy is again converted into mechanical motion of the same frequency through the transducer, which is then transmitted to the welding head through a set of amplitude transformer.The vibration energy received by the welding head is transferred to the joint of the workpiece to be welded. In this area, the vibration energy is converted into heat energy by means of friction to melt the area of the part to be welded.
Ultrasonic waves can be used not only to weld metals and hard thermoplastics, but also to process fabrics and films.
2. Principles of ultrasonic plastic welding
When ultrasonic wave acts on thermoplastic plastic contact surface, it will produce tens of thousands of high-frequency vibration per second. This high-frequency vibration reaches a certain amplitude, and the ultrasonic energy is transmitted to the welding area through the upper welding parts. Due to the large acoustic resistance at the interface of the two welds, local high temperature will be generated.
And because of the poor thermal conductivity of the plastic, it can not be distributed in time and gathered in the welding area, which causes the contact surface of the two plastics to melt rapidly. After adding a certain pressure, it will be fused into one.
When the ultrasonic wave stops acting, let the pressure continue for a few seconds, so that it solidifies and forms, so as to form a strong molecular chain, to achieve the purpose of welding, welding strength can be close to the strength of raw materials.
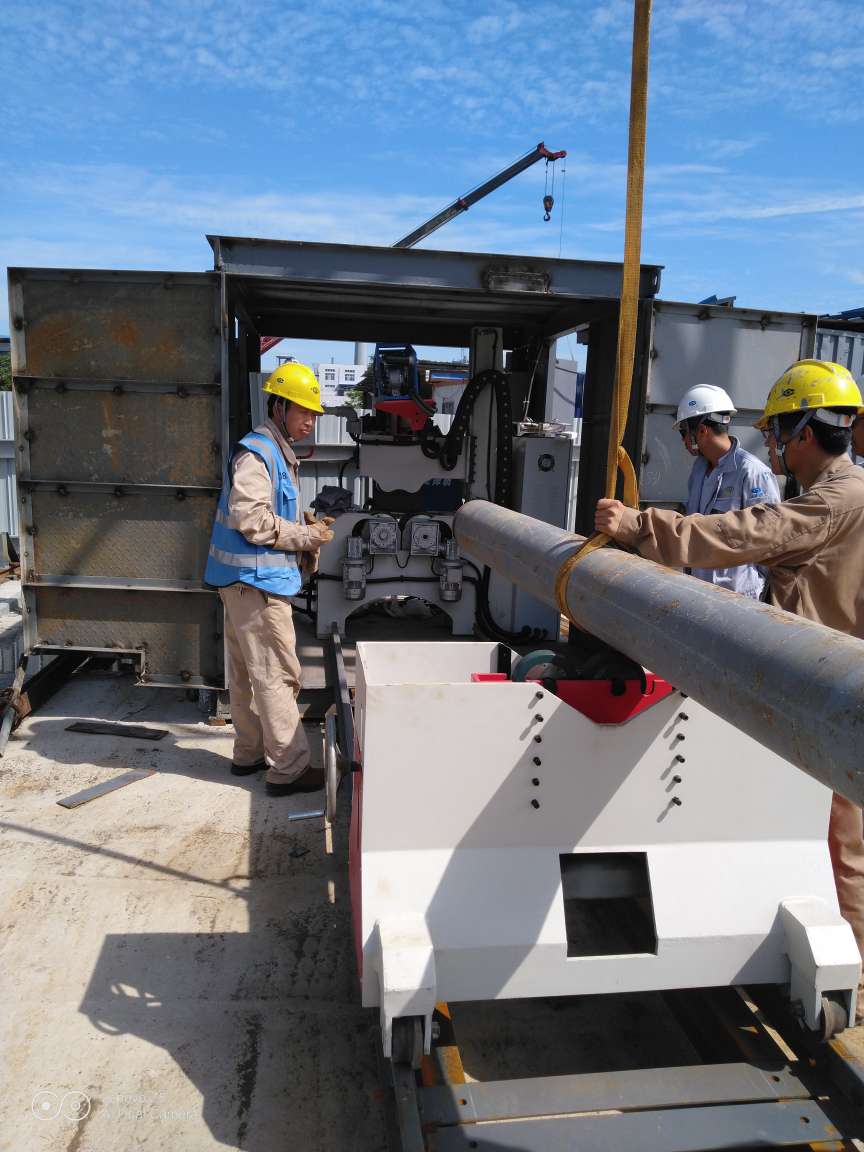
1. Advantages of ultrasonic metal welding
A, welding material is not molten, not fragile metal characteristics.
B. Good electrical conductivity after welding, very low or almost zero resistivity.
C. Low requirement on welding metal surface, welding can be done by oxidation or electroplating.
D, short welding time, without any flux, gas, solder.
E, no spark welding, environmental protection and safety.
For all application markets, ultrasonic welding has won recognition from all walks of life for its unique advantages: fast, efficient, clean and firm.